For a long time to show the main
application has been led demands for heat dissipation requirements led
the case is not very high, led more use of traditional resin substrate
package. After 2000, with the led high luminance and high efficiency of
technology development, coupled with significantly improved the
efficiency of blue light-emitting led, and led manufacturing costs
continue to decline, so that led range of applications, and are willing
to use led the industry continue to expand the scope of increase,
including liquid crystal, electrical appliances, automobile industry,
but also began to actively consider the possibility of application led,
for example, consumer products industry expectations for high-power led
is to achieve energy saving, high brightness, long life, high color
reproducibility This represents achieve high heat dissipation
capabilities, is a high-power led substrate indispensable conditions.
In addition, LCD panel makers to face the EU RoHS specifications, to
confront the cold cathode fluorescent lamp will be a comprehensive
mercury-based environmental pressures, creating a market for high-power
led needs were more urgent. In addition to protecting the internal
package led chip led, but also both led the chip with the outside to
make electrical connections, cooling and other functions. Epoxy resin
properties no longer meet the demand for high-power led 1 led to
achieve a few hundred lumens, which is basically not a big problem, the
main problem is how to deal with heat? Then in generating such a large
lumen, how to maintain the stability and continuity of brightness,
which is another important issue, if the heat did not do a good job,
then, led the brightness and lifetime will decline rapidly, for the
led, how to be effective, reliability and thermal conductivity, is very
important.
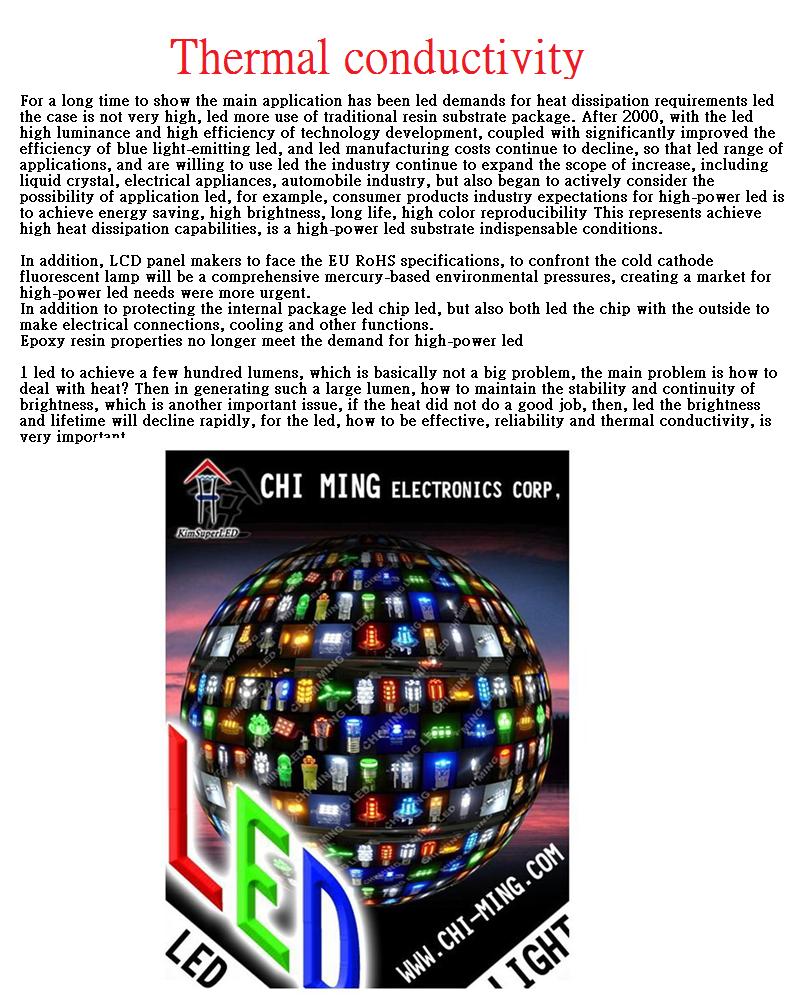
|