|
|
|
JINLING Chen
|
KIM Chen
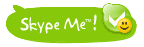 |
|
Subject: AUTO LED LIGHTING-FESTOON LED
|
2009-12-07 |
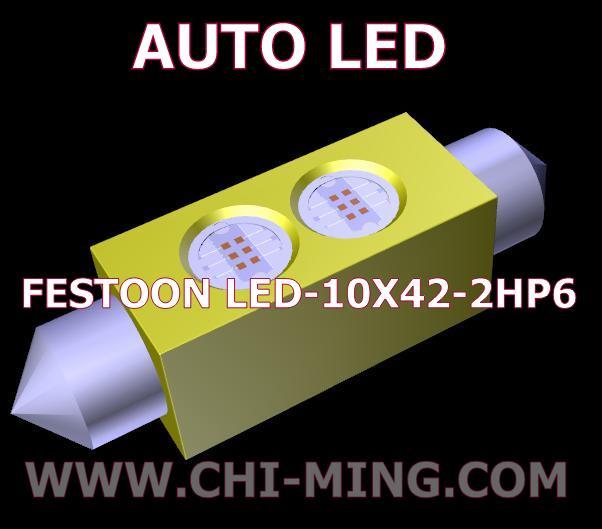
|
|
Heat
better with flat-type LED package and still increase the thermal heat
sink area, and even larger area of fins and fans, so that timely and
dissipation of heat generated to the atmosphere. Thermal substrate
according to materials can be divided into three major categories, less
than 1 watt power printed circuit board (FR4), power is greater than 1
watt metal cooling substrate, as well as higher-priced ceramic
substrates. Because traditional printed circuit board thermal
conductivity is low (mostly in the 0.5 W / mK or less), and the only
advantage of the increased thermal vias used in a limited degree of
improvement in heat dissipation, has been gradually cooling in
high-power LED market disappear. As the metal substrate and the ceramic
substrate with large thermal conductivity (aluminum, copper, alumina
and aluminum nitride thermal conductivity of approximately 170, 380,20
~ 40 and 220 W / mK), coupled with mass production yield upgrading of
high-power LED thus become the two main heat the substrate. In
addition, a machining of metal substrates, non-friable, low price and
other advantages, the development of more potential. Heat from the
metal substrate metal sheet (aluminum or copper), insulation layer and
the copper wire composition, thermal efficiency is the choice of
materials depends on the insulating layer and the substrate structure
design. Insulating layer of material with poor heat dissipation from
the early resin (thermal conductivity of 0.5 W / mK), and further add
the heat a good alumina powder or other metal oxides, so that thermal
conductivity up to 1 ~ 6 W / mK, and even to the anode oxide film (20 W
/ mK) or diamond films (~ 400 W / mK) to replace. However, the biggest
challenge is how to make the manufacturing costs and enhance the
reliability of insulating material. Is currently widely used metal
cooling substrate structure, is the use of thermoelectric separate
design, skillfully channels the heat in the insulating layer to remove.
By thermal glue (thermal conductivity of 1 ~ 2 W / mK) or tin alloy
(thermal conductivity of about 50 W / mK) the use, so that the bottom
LED and metal combination of greatly improved interface, thermal
conductivity, but this is not metal substrates for the bottom electrode
of a light-emitting diodes. Thermal substrate with circuit design, LED
and power size of the different types of design, reliability and price
of the product is to determine the thermal design of the most important
specifications. Taiwan light-emitting diode market value of the size of
plant second only to Japan, is the world's second-largest in the world
market share of more than two into. Because Taiwan has a complete LED
upstream and downstream industry chain, a strong material development
capabilities, with price-competitive printed circuit board industry, as
well as between industries mature foundry model for the future
high-power LED thermal technology are very favorable. In the optical,
electrical and heat transfer in three areas can be best resolved,
Taiwan in the 21st century in the history of the evolution |
|
|